In der Natur findet sich häufig eine spezielle Bauweise, die hohe Belastungen aufnehmen kann und gleichzeitig sehr leicht ist. So enthält ein mehrschichtig aufgebauter Insektenpanzer eine flächige sandwichartig aufgebaute Struktur. Das feste Material befindet sich in der äußeren Schicht und sorgt für Stabilität. Der Kern hingegen besitzt eine „luftigere“ Struktur, die ein minimales Gewicht garantiert.
PBS als Monomaterial für Sandwich-Bauteile
Nach dem gleichen Prinzip lässt sich dieser Leichtbaueffekt für tragende Bauteile aus PBS anwenden. Um das zu zeigen, werden auf einer Zwei-Komponenten-Spritzgießmaschine (Abbildung oben) im Technikum des Kunststoff-Zentrums in Leipzig gGmbH spritzgegossene Prüfplatten in Sandwichbauweise hergestellt. Sie bestehen aus einer kompakten Hautschicht und einer geschäumten Kernschicht. Beide werden innerhalb eines Produktionszyklus‘ in sehr kurzen Zeitabständen hintereinander in das Werkzeug eingespritzt. Das fertige Sandwichbauteil ist werkzeugfallend, wodurch der Prozess für die Großserie geeignet ist.
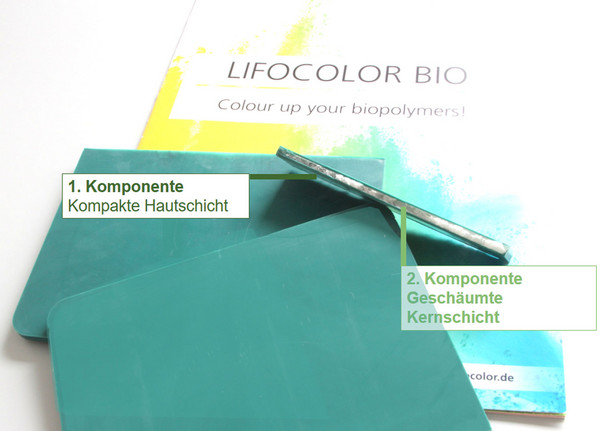
© KUZ Leipzig
Die Sandwichplatten bestehen aus einer robusten Haut und einer leichten Kernschicht. Obwohl sich die Schichten in ihren Eigenschaften und Funktionen stark unterscheiden, bestehen beide aus bioabbaubarem PBS. Diese Monomaterial-Konstruktion erleichtert die Wiederverwertung am Ende der Produktnutzungsdauer.
Den schichtweisen Aufbau regelt eine Sandwich-Zwischenplatte. Die Abbildung zeigt die Funktionsweise. Die Hautschicht wird als erste Komponente vom vertikalen Aggregat eingespritzt. Es folgt die geschäumte Kernschicht, die in der horizontalen Plastifiziereinheit mit Stickstoff als Treibfluid beladen ist.
Zur Anwendung kommen die PBS-Compounds BIO-ELAN A 022 und A140 HS1 der Merseburger Exipnos GmbH, die sich im Wesentlichen durch ihre Schmelzeviskosität unterscheiden. Für eine bessere Sichtbarkeit ist die Hautschicht mit einem Farbbatch auf PBS-Trägermaterial eingefärbt.
Die Zusammensetzung des Farbbatches gewährleistet eine Zersetzung in natürliche Verbindungen, so dass auch durch die Additivierung die Bioabbaubarkeit des Polymers vollständig erhalten bleibt und Mikroplastik erst gar nicht in die Umwelt gelangen kann. Die Materialzusammensetzung der Prüfplatten ist in der folgenden Tabelle zusammengefasst.
Versuch 1, bei dem Bio ELAN A 022 sowohl in der Haut- als auch in der Kernschicht verarbeitet wird, erzielt die höchste Gewichtsreduktion von 22 % im Vergleich zum kompakten PBS. Auch die Schaumstruktur ist homogener mit einer kugelförmigen, mechanisch günstigeren Blasenform. Die folgende Abbildung zeigt mikroskopische Aufnahmen der Schaumstruktur im Vergleich.
Für den zukünftigen Einsatz an technischen Bauteilen mit höherer Biegebeanspruchung könnte ein durch Naturfasern verstärktes PBS zum Einsatz kommen. Auch ein Hinterschäumen von Naturfaserlaminaten oder Tapes wäre denkbar. Besonders vorteilhaft wirkt sich die Gewichtsersparnis bei Bauteilen aus, bei denen eine Verringerung bewegter Massen erzielt werden kann. Industrielle Anwendungen wären beispielsweise Rotoren, Bürstenkörper, Trittstufen, Heckspoiler, Träger bzw. Auflagen und Roboteraufbauten.
Die Kunststoffzentrum in Leipzig gGmbH ist Mitglied im POLYKUM e.V.
Weitere Informationen erhalten Sie hier: